How Plug’s Customers Are Making Everyday Items Greener
Customers like SBB ENERGY S.A. are working with Plug to support a variety of technologies, including those that produce everyday consumer goods.
Opportunities for green hydrogen to help decarbonize the world are everywhere — including in the creation of the everyday consumer goods you use. Although there is a lot of excitement about the ability to use green hydrogen to produce electricity when the sun isn’t shining, or the wind isn’t blowing — green hydrogen can be used for so much more.
Although the focus has been on applications labeled as “Power-to-Power” and “Power-to-Gas,” Power-to-X is probably the least understood application but will drive a significant portion of the demand for green hydrogen in the near term. What does the “X” represent? You guessed it —everything else that isn’t covered in other applications.
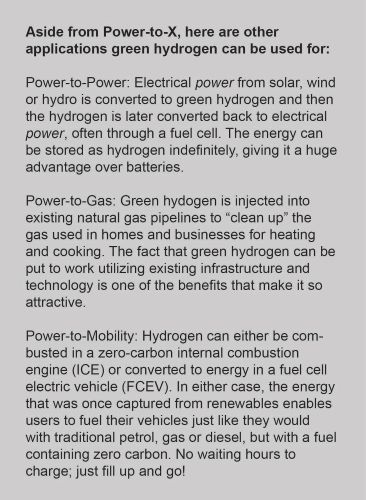
Hydrogen is already used in many processes to create everyday products like fertilizer, chemicals (ammonia and methanol), and plastics. It is even used in the process of oil refining. In all these cases, more than 95% of the hydrogen comes from fossil fuels, emitting millions of tons of CO2 per year — a devastating reality for the world we live in. This hydrogen is commonly known as grey (which is produced from natural gas) or brown (which is produced from coal). Simply replacing the grey and brown hydrogen with green as quickly as possible will make a major positive impact on the climate.
One exciting P2X application is using hydrogen in the process of making household goods. As consumers, many of us struggle with the fact that with almost anything we buy we are growing our carbon footprint. More and more, people are paying attention to how their goods are manufactured and are even willing to pay a premium to know that they were made in sustainable ways. Raw materials such as steel, glass, concrete, and plastics are heated to their melting points so they can be molded or crafted into all kinds of products. The heat used in the process most commonly comes from burning coal, wood, or a dirty gas. Manufacturers are beginning to turn to green hydrogen as an alternative. Like the other P2X applications, these manufacturing processes often run 24-7 and use a lot of hydrogen, making onsite electrolysis the way to go vs. trucking in liquid H2.
Promet-Plast, a manufacturer of plastic medical equipment, with the support of SBB ENERGY S.A. and Plug, is leading this early adoption effort. Promet-Plast has been working to make their operations more sustainable for years and has made significant investment in renewable energy. Today, it has Poland’s first medical equipment manufacturing plant with zero CO2 emissions technology.
In 2021, SBB ENERGY S.A., an energy solutions provider for traditional and emerging companies, won a bid to design and construct a high-efficiency trigeneration plant to create heat, cooling, and power for a Promet-Plast manufacturing plant. Project requirements included the ability to provide up to 90 kg per hour of hydrogen that will either be compressed to 500 bar and stored or directed to a CHP (combined heat and power) engine capable of running on 100% hydrogen. In addition, the plant will deliver up to 1 MW of electricity and 1.2 MW of heat or cooling from the absorption chiller.
Having operated in the power and industrial sectors since 1992, SBB ENERGY S.A. has the knowledge and experience to execute on this forward-thinking vison for a manufacturing plant fueled by clean hydrogen. The operation requires a constant supply of hydrogen at high availability and a technology that can ramp up and down instantaneously. SBB ENERGY S.A. selected Plug to provide the 5 MW PEM electrolyzer that will keep Promet-Plast’s plant up and running not just because of the technology fit, but also Plug’s bankability and track record of putting the customer first. Only Plug has the resources for a project of this scope, having been the fastest to market with a 5 MW containerized PEM electrolyzer solution. Plug already has a 5MW PEM electrolyzer operating at its first green hydrogen production plant in Kingsland, GA in the USA. That system went from concept to in the ground in less than a year, speaking to Plug’s ability to move quickly.
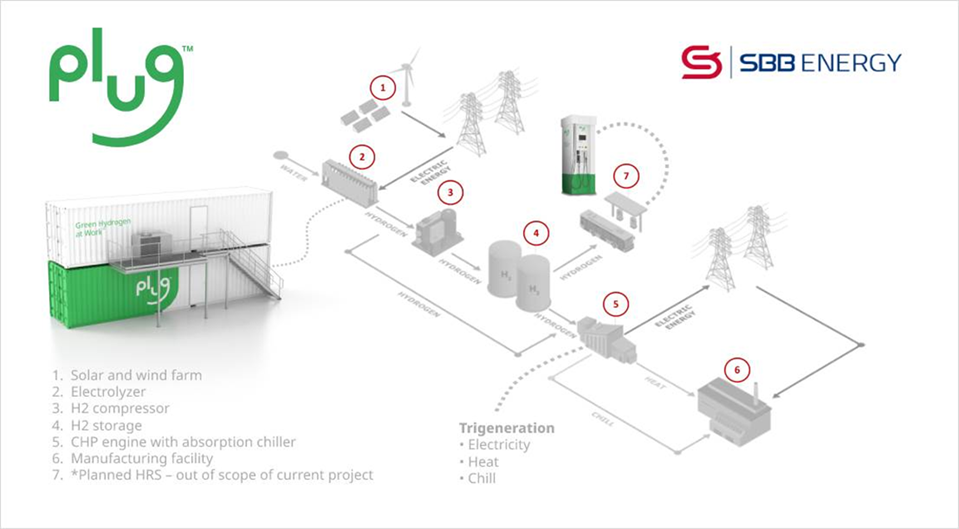
The 5MW Plug electrolyzer for SBB ENERGY S.A. and Promet-Plast is currently in production and will be the first of its kind to be integrated and commissioned by the Plug Systems Solutions team in Amsterdam later this year. Plug’s team of more than 300 engineers in Europe fully dedicated into the H2 market brings the expertise to execute on projects of all scopes and sizes. Collaboration with customers like SBB ENERGY S.A. on projects like this trigeneration plant for a Power-to-X solution is what Plug is all about.
The post How Plug’s Customers Are Making Everyday Items Greener appeared first on Plug Power.