Between Two Stacks: How a PEM Electrolyzer is More Cost-Effective Than an Alkaline Electrolyzer
Many corporations and governments have committed to decarbonizing the processes that use grey hydrogen (sourced from fossil fuels) – like oil refining, or ammonia and methanol production – which are all spiking in demand as population increases and developing countries industrialize. The demand for increased electrolyzer capacity in the immediate term will come from easily decarbonizing these emissions-intensive processes with drop-in green hydrogen supply.
However, it can be difficult to determine what type of electrolyzer is best to power your business operations — especially with the rapid advancement in technology.
The two predominant electrolysis stack technologies today are a PEM electrolyzer (proton exchange membrane) and an alkaline electrolyzer. Although Plug believes both have a space in the hydrogen economy, this blog will clarify the economic impact when using a PEM electrolyzer compared to an alkaline electrolyzer, including the initial investment and the cost of maintenance over time.
Here’s how the stacks compare to each other.
Between a PEM Electrolyzer and an Alkaline Electrolyzer
Alkaline electrolyzers may seem like the most affordable option — after all, alkaline has been around for decades longer than PEM. However, progressions in PEM technology have changed its cost.
An analysis of both types of electrolyzers shows that the stack cost of an alkaline electrolyzer is lower than PEM. But when it comes to the complexity and cost of balance of plant (BOP) as the system size increases, PEM is lower, according to the Fraunhofer Institute for Solar Energy Systems ISE. In fact, the total cost of ownership of a PEM electrolyzer is lower than alkaline with forecasters estimating that PEM service costs are one-third of alkaline.
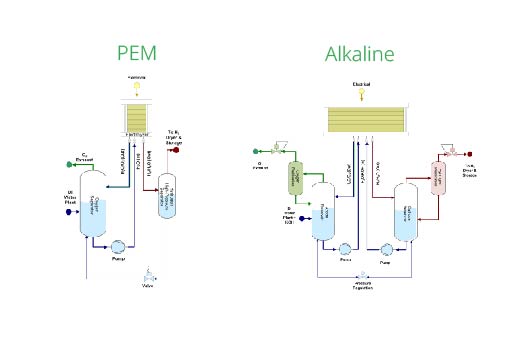
When scaling an electrolyzer, PEM has significant cost advantages in balance of plant economics. On a per-kilowatt basis, the capital expenditure associated with an alkaline electrolyzer increases significantly as the system scales. With PEM, there are options for streamlining BOP to minimize upfront cost in larger systems above 10 megawatts.
When considering output pressure, standard alkaline electrolyzers deliver output at a low pressure of 1 to 10 bar, which is a nearly ambient pressure. For most applications, hydrogen must be further compressed for transport, storage, or consumption. On the flip side, Plug’s PEM electrolyzers have an output of 40 bar — that’s 4 to 40 times of a typical alkaline system.
Pressure is generated by the electrochemical process in the stack, meaning PEM avoids first stage compression to bring it up to 40 bar, and bypasses the energy costs associated with compressor operation.
Alkaline’s caustic electrolyte solution can also ratchet up its hefty price tag. For example, a 10 to 20-year-project means a long term need to replace parts such as pumps and valves, or the removal of potassium hydroxide from the hydrogen or oxygen streams. The 3.5 ton per megawatt requirement for highly-corrosive potassium hydroxide in alkaline systems typically incur significant space requirements – often two to three times the space of Plug’s PEM system for a similar output. Any losses in space can lead to losses in revenue.
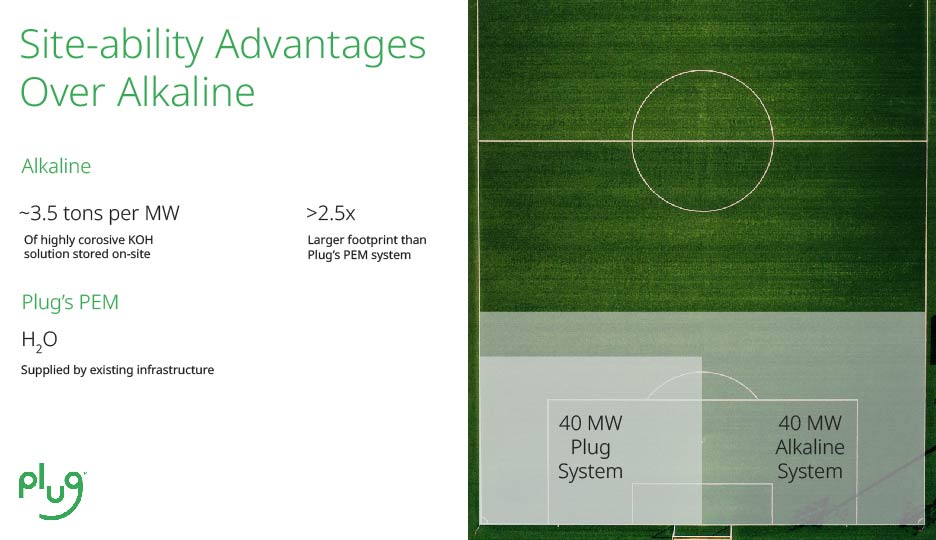
Finally, the cost of safety is another measurement businesses should consider. Increased safety concerns with alkaline electrolyzers lead to more required safety equipment, labor, permitting, and compliance costs for businesses, and worst of all, putting worker well–being at risk. With PEM electrolyzers, technicians and operators only deal with one “chemical” while working on PEM systems – water.
This is just the beginning of the cost differences. However, analysts believe that technology will only improve the costs of PEM electrolyzers while alkaline technology has already achieved most of its potential cost reductions.
Market Growth for Electrolyzers
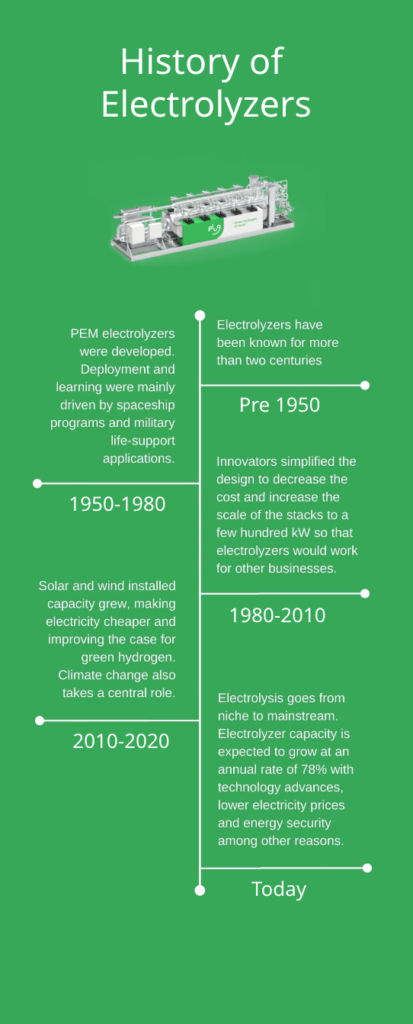
Global electrolyzer capacity is expected to grow at a compound annual growth rate of 78% over the next decade, rising from 0.5 gigawatts (GW) of installed capacity in 2022 to 84.7 gigawatts in 2031, according to a March 2022 report from Guidehouse Insights, a marketplace advisory firm that covers the energy industry.
The International Renewable Energy Agency noted in 2020 that the post-2020 generation of electrolyzer projects are expected to move from niche to mainstream and escalate from megawatt to gigawatt in scale. Industry’s goals are to reach lower cost, higher durability, and higher efficiency for electrolyzers over time, which will require scaled production, more manufacturing power, and research-driven technological advancements.
Plug is Paving the Way with PEM Electrolyzer Technology
Plug is utilizing its own PEM electrolyzer technology to build out North America’s first end-to-end green hydrogen production network, with an estimated 565 megawatts of product being installed across this network today at plants in Georgia, New York and Texas, and more capacity to come into the network in future phases.
Looking more broadly across the globe, by 2025, Plug will have electrolyzer projects ranging from 1 megawatt to 1 gigawatt deployed across five continents helping to decarbonize a multitude of applications, including refineries, chemical and fertilizer production, manufacturing and heavy industry, heating homes and buildings, and powering fuel-cell electric vehicles. That’s right – 1 gigawatt.
Some of the biggest electrolyzer projects Plug is working on include an order for a 1 gigawatt PEM electrolyzer with H2 Energy to produce 432 tons per day of green hydrogen using offshore wind in Denmark. In partnership with Fertiglobe’s Green Hydrogen Consortium, Plug is also the technology provider for a 100 megawatt PEM electrolyzer project in Egypt to produce green ammonia.
This is just the tip of the iceberg as more business and government leaders look for clean energy solutions that can be produced locally and independently from the grid. Plug is proud to the lead the way.
Interested in exploring how Plug can help your company improve operations with our best-in-class green hydrogen electrolyzer products? Contact us today.
Join us for a webinar on July 26 as Plug EVP David Bow discusses both stacks. Register for the free webinar here.
The post Between Two Stacks: How a PEM Electrolyzer is More Cost-Effective Than an Alkaline Electrolyzer appeared first on Plug Power.